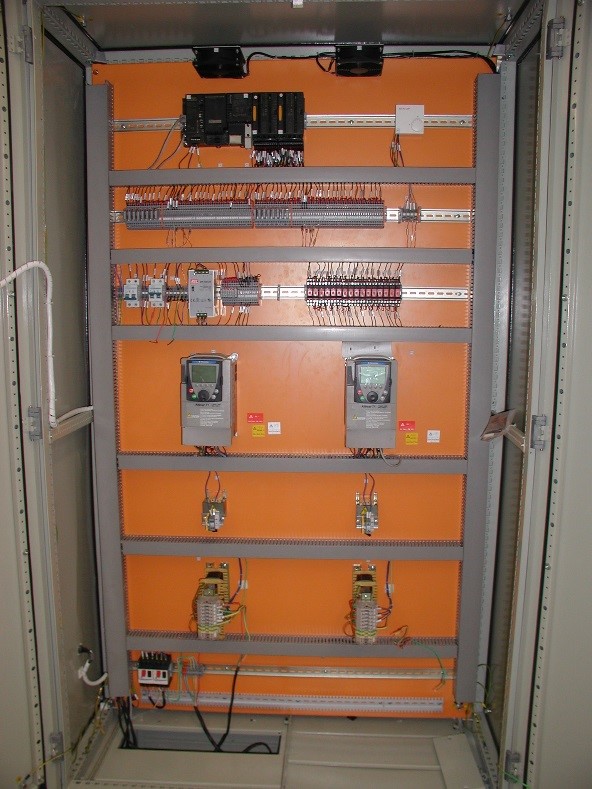
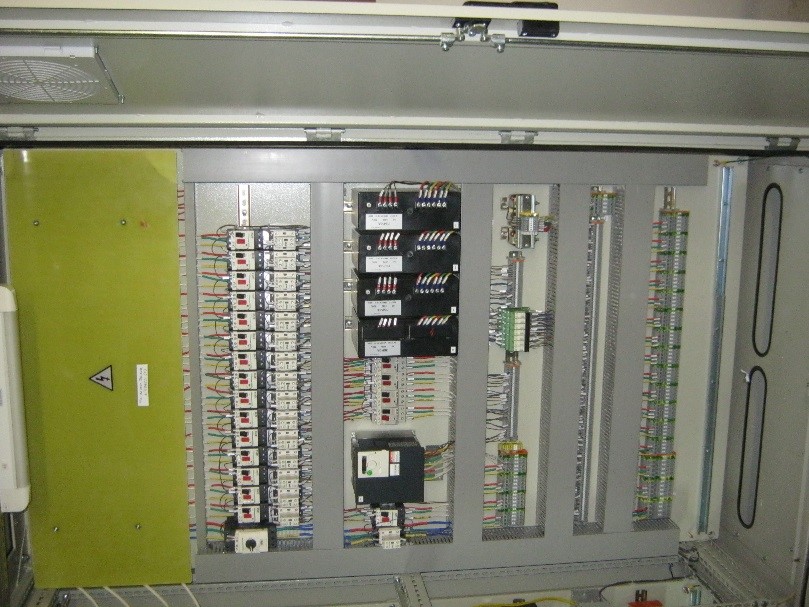
Motor Control Cabinets
MCC’s are designed to operate motors and electrified valves. Direct-on-line and reverse starters, soft starters and frequency-to-voltage converters are used to operate electric motors. The branded devices of original equipment manufacturers Schneider Electric, Siemens, General Electric are used as protection, communication and control devices.
To prevent damage motors are equipped with motor protection circuit breakers, thermal releases, motor controllers, as well as a built-in soft starters and frequency converters.
To control an electric motor typical circuit diagram of embedded system is provided in two modes: local (from the local control panel without PLC) and remote (using PLC). The motor state resulting data are available in both modes on PLC. If required, PLC can be adapted to stop the motor in local mode (for example, local mode can be set when liquid is pumped into the tank, the liquid level is monitored by PLC and a pump shuts off when the tank is full).
Valves are controlled by reversing starters, solid state relays or SSCs (solid-state contactors). Motor protection circuit breakers and thermal releases protect against overloads.
Typical valve control circuit provided in the control cabinet includes two control modes: local one (from the local control panel without PLC) and remote (using PLC). PLC evaluates valve status data in both modes. The control circuit turns off the valve drive with a limit switch actuated to open and closed position, or a valve torque limit switch (closing with tightening).
Feedback circuits receiving data from valve positioner, either pulse control or analogue signal control with apart power supply to the valve are used for regulated valves. Valves with pneumatic actuators are quite similar in design.